Highlighting the medical applications of 3D printing in Egypt
Introduction
3D printing is the common name of the layer-based manufacturing technique that transfers computer-assisted designing (CAD) models directly to real physical products by deposing and jointing material layers ending up with dense, hard and complicated structures resembling those of the computer numerical control (CNC) and traditional methods (1). It was developed to provide rapid prototyping in a short time, with minimal human intervention and least material waste (2).
There exist several 3D printing techniques based on the working method and material used. For example, manufacturing of metals uses high-power laser or electron beam to selectively melt and joint stacked metal powder layers, controlled by digital software (3). Another technology for building up metallic models is the so-called 5-axis-milling technique that can melt, cut and shape different metallic alloys (4). For plastic models, low-power lasers, UV light, thermal or chemical bonding are commonly used to shape the hard plastic products out of raw liquid, powder or filaments.
3D printing has become very important in the medical field as it could produce material with high biocompatibility, withstanding high pressure and temperature to be sterilized and autoclaved. It enabled medical practitioners to produce appliances tailored for each patient’s morphological and functional needs (5). In orthopedics and maxillofacial surgery, the technology has helped in the production of surgical guides, templates, splints and cutting tools in a time-saving and cost-effective way. It has also been involved in several cases such as complex bone fractures and joint replacement as it merges digital imaging with 3D designing. Other surgical applications of 3D printing are the production of by-pass systems together with patient-specific artificial vasculature and 3D-printed transplants which now enforce physicians and surgeons to develop completely 3D-printed organs (e.g., heart, liver and pancreas) (6).
This paper presents an experience from a developing country (Egypt) on the use of 3D printing technology in the medical field.
The medical use of 3D printing
The medical 3D-printed products, unlike industrial and educational products, are used in contact with human body: bone, soft tissue and blood. That is, the material should be safe for human and does not contain toxic or cancerous elements. There is a wide range of materials including Ti6Al4V, Ti6AL4N, polyamide PA2201, stainless steel 316L, hydroxyapatite and calcium phosphates powders used for medical applications. These products should be handled in a clean and sterile environment and some products should have extra stability to withstand autoclaving and/or chemical sterilization. The ASTM or ISO medical standard specifications should be followed to eliminate legal responsibility of the medical practitioners. Also, high geometrical and dimensional accuracy is required as any small deviation from the original design may result in healing delay or unexpected side-effects, especially in maxillofacial and spine surgeries (7).
3D printing is increasingly demanding in the medical field as it could facilitate good diagnosis, preoperative planning and communication between colleagues and patients. It could also create tangible models from medical imaging data (e.g., CT and MRI) that has proven highly advantageous, especially within the field of craniofacial surgery where planning and performing operations is extremely difficult due to the complex and variable anatomy. The technique has the ability to produce complicated shapes and geometries in small size and fine tolerance that fit anatomy and morphology (8).
The introduction of medical modelling has proven useful in terms of visualization of the patient’s anatomy before surgery which, in turn, allowed for simulation of surgery before intervention. It also allowed for creating custom implants, templates or guides prior to surgery and improved the communication between doctors and patients (Figure 1) (9).
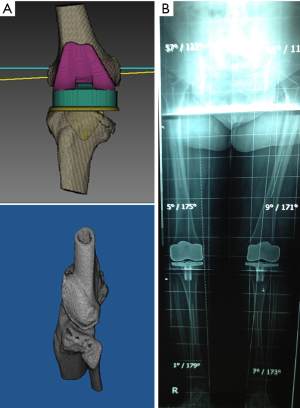
Although the modeling process can be done with high range of accuracy (reproducing CT data to a tolerance of 0.1 mm), there are still concerns over the wide use of this application related to some uncontrollable errors (5). The major source of error could the scanning process itself, where inaccuracies of up to 0.5 mm may occur. This type of error composes an obstacle for surgeons while being challenged by complex congenital deformity, traumatic reconstructive procedures or joint revision surgery. Thus, accurate planning of surgery together with practicing osteotomy cuts and fabricating plates, implants or prostheses could be difficult (10). In fact, the aim of practicing the procedure in vitro is to reduce the operative time and improve the results. Similar geometric problems are encountered in cranio-maxillofacial surgery where re-establishing the dental occlusion and facial contour of a millimeter is important (10).
Technical and clinical development
3D printers are frequently modified to add more features such as the ability to produce complex tools with hybrid materials. The so-called desktop 3D printers mimic the office PC printers and can be purchased by hospitals and stored inside operating rooms, radiology departments or outpatient clinics. This allows imaging, planning and instrument production to be done at one site, saving time and resources. Other imaging modalities are currently used, such as 3D radiographic X-ray or cone-beam CT (CBCT) to produce best-fit appliances (11,12). The printing materials are continuously developed to become durable and inexpensive.
Current clinical trials adopt a graduate approach and early learning curve, that is, medical practitioners can perform different procedures based on computer-assisted designing/computer-assisted manufacturing (CAD/CAM) technique and apply the outcome on real patients. They can position 3D-printed templates on bone, teeth or other structures to test the accuracy of positioning, to mark the level and inclination as well as to evaluate the physical and biomechanical properties of such templates. Most of surgeons have now developed confidence with this technique, so it can be used for different procedures without resorting to conventional instrumentation or techniques. It is worth mentioning that conventional surgical techniques had some sort of difficulty when dealing with vital or complex structures; meanwhile, the conventional techniques have some limitations when used with patients with poor medical condition or bleeding tendencies.
Medical 3D printing in Egypt
3D research work has started in Egypt since 2004 by the first dedicated Rapid Prototyping and Manufacturing Research Laboratory in the Central Metallurgical R&D Institute (CMRDI) (www.rpcmrdi.org). Today, there is noticeable development in the implementation of medical 3D printing in Egypt and there are many recorded cases for patients who have recovered through 3D-printed solutions (13). Due to the high capital cost of the 3D printers, only a few machines are available in public institutions in Egypt and most of them are from the small-size category (desktop machines). Table 1 summarizes the available 3D-printing systems in Egypt in addition to a number of cases done on this system; Table 2 describes the current state of using medical 3D printing in Egypt.
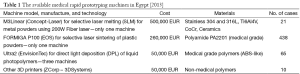
Full table
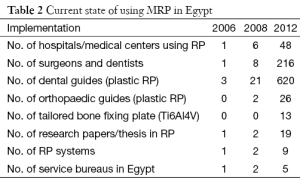
Full table
In 2011, Egypt had many incidents that increased violence and accidents, and many patients have been suffering from complicated and progressive fractures especially in maxillofacial region that influenced the need for 3D printing. Many procedures needed surgical guides and implants for fixation of zygomatic fractures (cheek bone), especially those with complete deformation of the face side bone which had to be reconstructed symmetrically to the healthy side of the face. Also, many incidents needed surgical guides and templates for incorrectly healed bones that had to be separated and rejoined correctly. Other crucial procedures were implant-supported partial or complete maxillary and mandibular prostheses as well as customizing Ti6Al4V meshes and bone fixing plate for reconstruction of facial injuries. Such procedures were done with metallic implants which had mesh structure with 60% porosity to reduce their weight and allow good osteointegration.
3D printing in Egypt has been mainly focusing on fabricating surgical guides and stents for completely or partially edentulous patients that need customized dental implant designing (Figure 2); it is also majorly used to fabricating patient-specific templates for total knee arthroplasty (TKA). It has also been used for the production of models for different bony structures for educational purpose.
In another study related to 3D printing in Egypt, it was found that the technology enabled manufacturers to produce high-value objects with accurate designing, giving the opportunity of producing medical instruments and laboratory tools in addition to vaccination beads and prosthetic appliances. Thus, it could promote higher living standards and improve the quality of healthcare in this country which has almost 90 million inhabitants (5). This study had similar observations of our study. It focused on the economic consideration of using 3D printing in medical industry. The authors have found that plastics are the commonly used material for the printing jobs; however, attempts are continuing toward manufacturing metal objects in an affordable way. There is an increasing demand to reduce the cost of the currently used plastics and to eliminate material waste. This goal could be achieved by recycling material waste with special heat-treatment method. In Egypt, there are concerns related to carbon emission from industrial factories and the relatively high shipping costs, and 3D printing could be very helpful to overcome such concerns provided that 3D printers and printing material become more commercially available in a cost-effective manner.
Soliman et al. studied the applications of 3D printing in urology and how the technology could improve the current treatment status quo. It was found that 3D printing is capable of creating massive change in urological surgeries. The capability of 3D printing to produce organ transplants will overcome the challenge of finding kidney donors and will aid in procedures such as bladder transplantation (14).
Another study evaluated different classes of hydrogels as scaffolds for 3D-printed cardiac tissue engineering. The used hydrogels were highly customizable with a range of components and techniques. This work has described the available approaches for fabricating such scaffolds, the recent designing criteria along with the challenges and limitations toward producing efficient hydrogel scaffolds in tissue engineering (15). Similarly, in light of tissue engineering, tubular scaffolds were fabricated with PLA material with fibrous morphology. These tubular scaffolds showed aligned fibers and even distribution of overlying layers of tissues and revealed shape recovery with compression testing. Such scaffolds and tissue-engineered assemblies could aid in the production of human osteocytes, chondrocytes and fibrocytes which are all necessary in cases such as osteosarcoma. They could also be utilized for cell-guided proliferation applications for tendon or ligament repair or as an optimal treatment of nerve injuries (16).
Different materials were employed in TKA surgeries with no complications were reported related to the type of material (Table 3) (10). That is, neither the bulk material nor their debris is harmful; also, the risk from immunological or physical hazards from this debris is not proven.
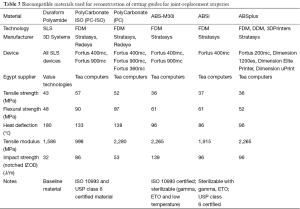
Full table
Conclusions
A wide range of dentists and orthopaedic surgeons has benefit from medical 3D printing technology in Egypt since 2004. The fast and accurate fabrication of physical products from biocompatible materials has become applicable; and the production of patient-specific surgical guides, templates and implants from the patient’s CT images has become easier. The technology has been implemented widely and successfully in Egypt as it helped physicians to tailor their treatment plans and improve the healing process for the patients.
Acknowledgements
None.
Footnote
Conflicts of Interest: The authors have no conflicts of interest to declare.
References
- Wohlers T. Wohlers Report (2010): State of the Industry: Annual Worldwide Progress Report. Wohlers Associates, Inc.: Colorado; 2010.
- Gibson I, Rosen DW, Stucker B. Additive Manufacturing Technologies: Rapid Prototyping to Direct Digital Manufacturing. Dordrecht: Springer Science & Business Media; 2009.
- Abdel Ghany K, Moustafa SF. Comparison between the products of four RPM systems for metals. Rapid Prototyp J 2006;12:86-94.
- Dewidar MM, Lim JK, Dalgarno KW. A Comparision between direct and indirect laser sintering of metals. J Mater Sci Technol 2008;24:227-31.
- Ibrahim AM, Jose RR, Rabie AN, et al. Three-dimensional Printing in Developing Countries. Plast Reconstr Surg Glob Open 2015;3:e443. [PubMed]
- 3D Printer Benchmark: New report measures speed, cost and quality of 3D printers. Available online: http://www.tagrimm.com/benchmark-2010/index.html
- Hao L, Dadbakhsh S, Seaman O, et al. Selective laser melting of a stainless steel and hydroxyapatite composite for load-bearing implant development. J Mater Process Technol 2009;209:5793-801.
- De Beer N, Dimitrov D, Van der Merwe A. Manufacturing of custom-made medical implants for cranio / maxillofacial and orthopaedic surgery - an overview of the current state of the industry. Journal for New Generation Sciences 2008;6:1-15.
- Available online: http://www.medicalmodeling.com/
- Hafez MA. Patient specific instrumentation: The past, the present and the future. In: Thienpont E. Improving Accuracy in Knee Arthroplasty. New Delhi: Jaypee Brothers Medical Pub, 2012;149-68.
- Vermeulen M, Claessens T, Van Der Smissen B, et al. Manufacturing of patient-specific optically accessible airway models by fused deposition modeling. Rapid Prototyp J 2013;19:312-8.
- Stoker NG, Mankovich NJ, Valentino D. Stereolithographic models for surgical planning: preliminary report. J Oral Maxillofac Surg 1992;50:466-71. [PubMed]
- Hafez MA. The use of computer-assisted orthopaedic surgery in complex cases of hip and knee arthroplasty: experience from a developing country. Biomed Tech (Berl) 2012;57:301-6. [PubMed]
- Soliman Y, Feibus AH, Baum N. 3D Printing and Its Urologic Applications. Rev Urol 2015;17:20-4. [PubMed]
- El-Sherbiny IM, Yacoub MH. Hydrogel scaffolds for tissue engineering: Progress and challenges. Glob Cardiol Sci Pract 2013;2013:316-42.
- Hossain KM, Zhu C, Felfel RM, et al. Tubular Scaffold with Shape Recovery Effect for Cell Guide Applications. J Funct Biomater 2015;6:564-84. [PubMed]